Are you looking to enhance safety and efficiency in your Behavioral Health or Geriatric facility?
At Kingsway Group, our 7-Step De-Risk Process is designed to meet those needs. In our previous blog, we explored the first phase of our De-Risk Process, the Relationship phase, and the benefits it brings in ensuring the optimum safety solutions are implemented for the unique needs of your facility, staff, and clients.
Today, we turn our attention to phase two; the Project Lifecycle. Here we implement the learnings gathered thus far in the De-Risk Process and transform them into tangible outcomes to minimize patient and staff safety risks. Kingsway’s in-house Project and Design teams collaborate with you to define the unique scope of your project before production begins in our Michigan-based manufacturing facility.
This phase is executed meticulously with the finest attention to detail as we draw on our experience gained in successfully delivering over 10,000 risk-reducing projects worldwide.
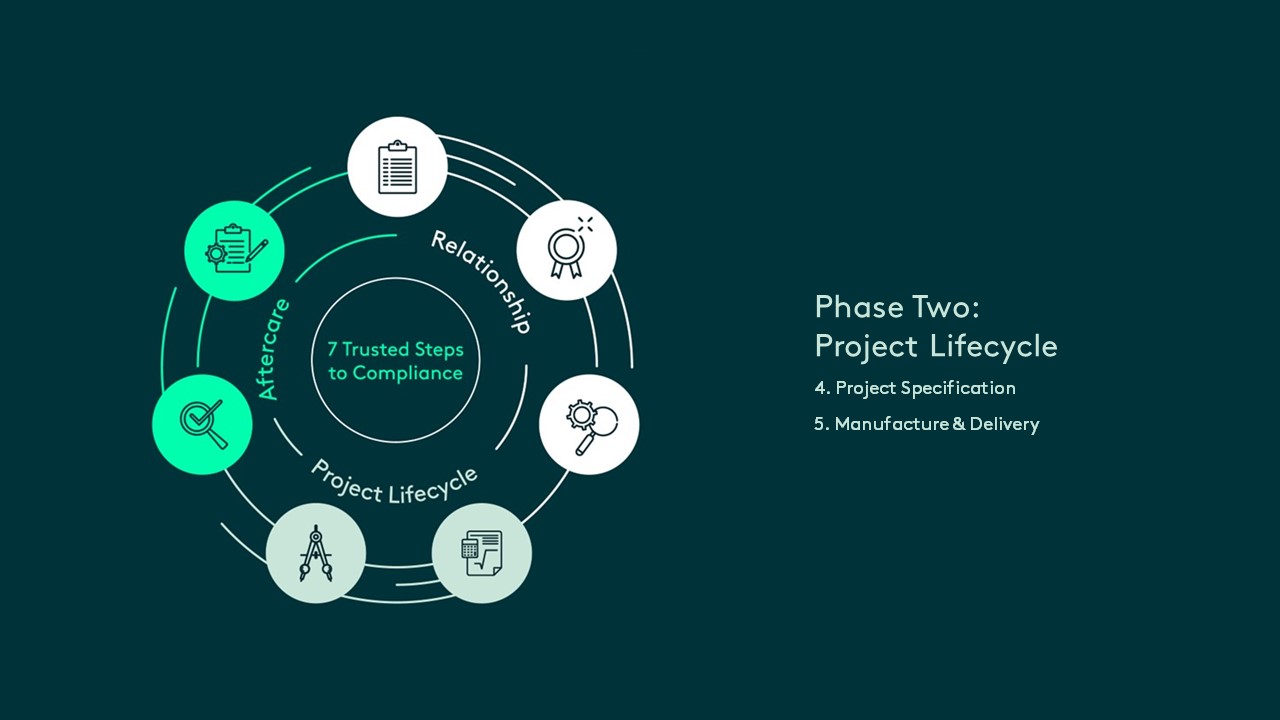
Understanding the Project Lifecycle
The Project Lifecycle is a critical phase in our 7-Step De-Risk Process that focuses on turning the strategies and best practices established during phase one into actionable solutions. It encompasses every detail from the initial concept to the final installation, ensuring that each step is planned and executed to meet the needs of your behavioral health facility.
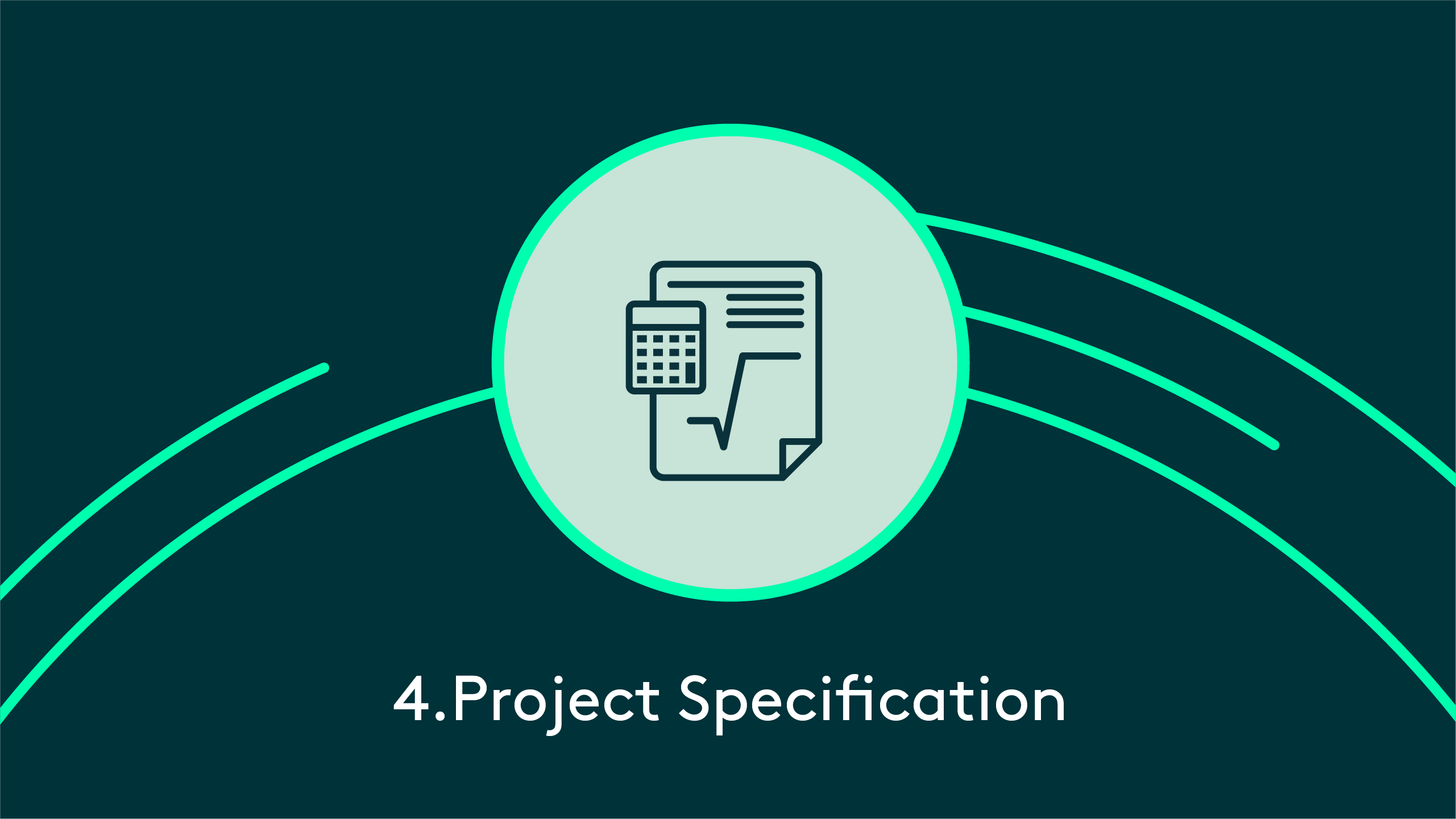
Project Specification: defining and meeting the project scope
The Project Lifecycle phase begins with step-4 of the De-Risk Process; the Project Specification. During this stage we collaborate closely with the key stakeholders, such as facility managers, clinical staff, architects, and more to define the scope of the project and develop a comprehensive specification tailored to your facility’s unique requirements.
The in-house Project and Design team at Kingsway Group focus intently on making sure all elements of the project work harmoniously and ensuring that every solution aligns with the industry standards and upholds the specific safety criteria crucial to your environment.
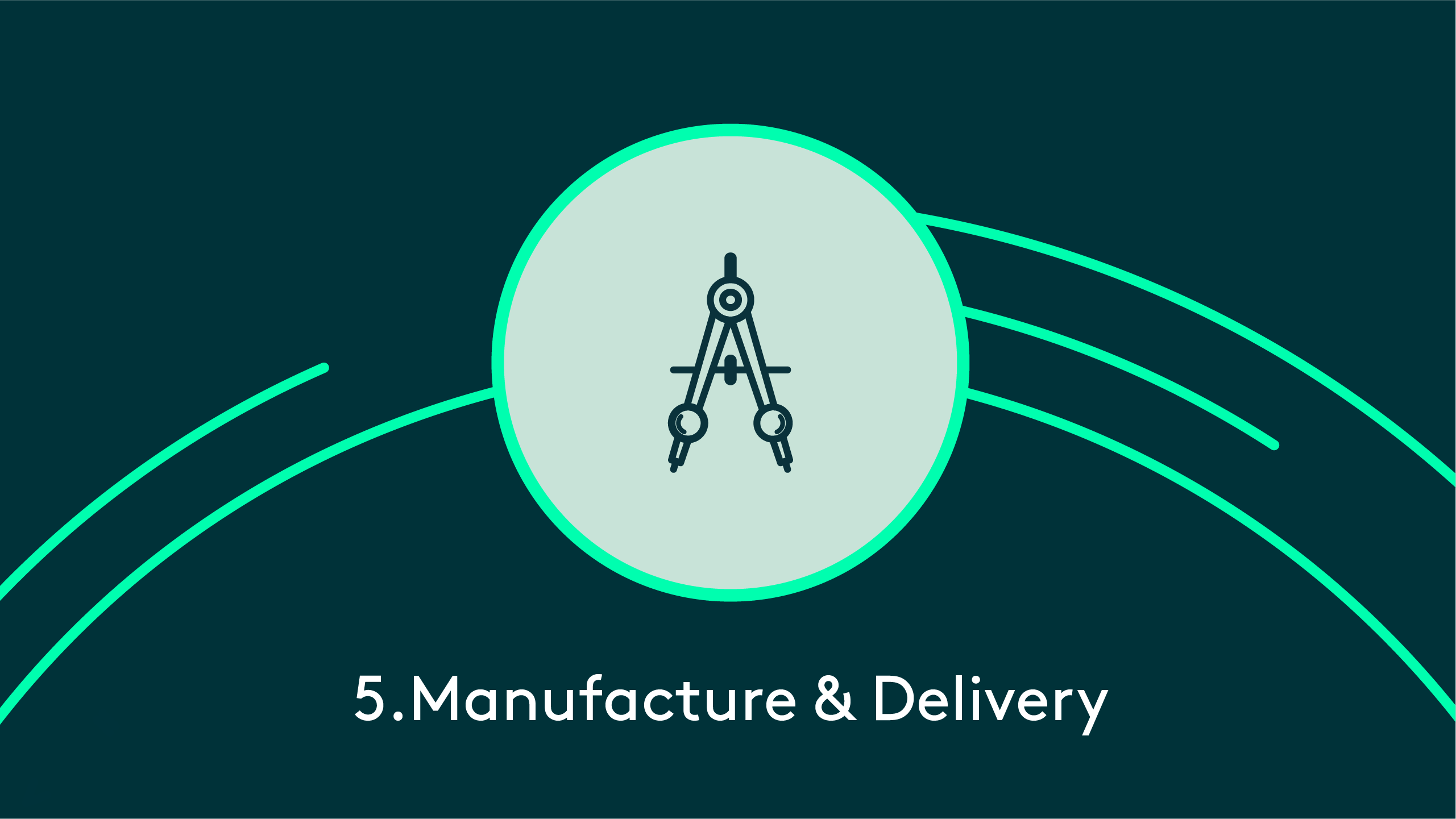
Manufacture & Delivery: Ensuring Quality and Timeliness
Step-5 of the De-Risk Process, Manufacture & Delivery, is where your project is brought to life. At this stage, Kingsway works diligently to ensure your products are produced to exacting standards to deliver quality and assured performance in the most challenging environments. Meticulous attention is given to each component as we fabricate your custom solutions in our Michigan-based production facility.
The Kingsway Group commitment to excellence is evident in every stage of production, from material selection to final assembly, ensuring that our ligature-resistant solutions are reliable, durable, and tailored to specific needs of your facility.
Once your solutions are manufactured and have passed a strict quality control procedure, they are prepared for delivery to site, ready for smooth and efficient installation. Our approach during this step of the De-Risk Process minimizes the risk of delays or defects, facilitating a smoother transition to the installation phase.
We understand the importance of accuracy and efficiency, which is why your Kingsway Project Manager remains available for site visits and project meetings throughout the process, ensuring any potential challenges are proactively addressed. This hands-on approach helps maintain the smooth running of the project and installation phase. By aligning every aspect of the Manufacture & Delivery with the standards established earlier in the process, we can best support the overall mission for improved safety of your facility.
Real-World Application: Success Stories
Our ability to provide tailored, high-quality solutions that meet the specific needs of behavioral health environments has consistently proven beneficial. A great example of the Project Lifecycle phase in action is at the Pontiac General Hospital in Michigan.
As part of a comprehensive renovation of the 6th Floor South Wing of their Adult Psychiatric and Behavioral Health Unit, Kingsway Group’s SWITCH Anti Barricade Doors and SOLO Single Action Doors were specified to enhance safety and functionality. One of the standout benefits of working with Kingsway Group was our ability to deliver fully pre-assembled door systems, which allowed for quick and efficient installation on-site. This streamlined process minimized disruption to the hospital’s daily operations and ensured a smoother renovation, aligning perfectly with the timeliness and safety standards set out during the initial planning phases.
Additionally, the Pontiac General Hospital was able to leverage their existing door frames, helping to reduce the installation cost. The flexibility of our systems to integrate with existing infrastructure is just one of the many reasons clients like Pontiac General Hospital choose Kingsway Group. This project not only improved patient and staff safety but also optimized operational efficiency, demonstrating the real-world benefits of the Project Lifecycle phase in delivering a successful renovation.
Conclusion
Navigating the complexities of renovation or new construction projects within the behavioral health space requires project partners who understand the unique demands of these environments and the importance of safety and compliance.
As Your Partner in Patient Safety, our detailed approach to each phase of the Project Lifecycle – from specification to manufacture and delivery – ensures your project meets and exceeds the high standards set out from the start.