- General
- 1 min read
De-Risking Mental Health Environments
Working collaboratively with some of the world’s leading mental health organisations, Kingsway continuously innovate at the forefront of anti-ligature product design and manufacture, de-risking for our clients at every stage.
Our approach takes a holistic view, working step-by-step to reduce risk for our clients across each area. This comprehensive program is designed to deliver peace of mind in high risk and unpredictable environments.
Potential risk exists in the following areas…
Patient Self-Harm
- The risk of patient self-harm or loss of life and the potential for litigation
Staff Injury
- The risk of harm to staff and the potential for litigation around violent incidents or injury
Non-Compliance
- Accreditation issues due to poor ligature mitigation and risk control
Slow Patient Recovery
- Poorly designed environment impacts patient recovery times and damages hospital reputation
Under (or over) Specification of Product
- Unsuitable products leading to financial loss and health & safety issues
Incorrect Assembly of Product
- Leading to safety concerns, damage, litigation, and financial loss
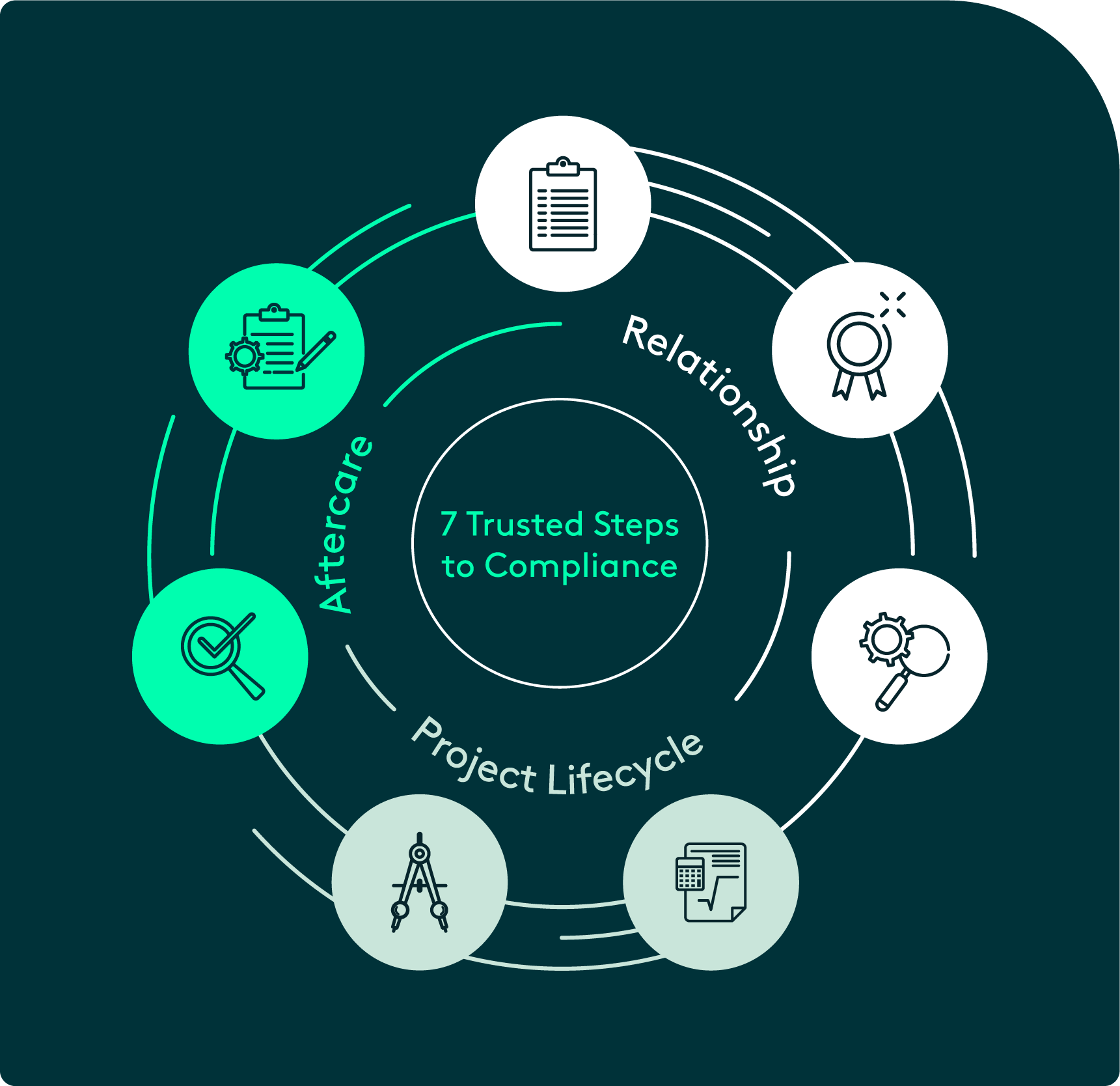
The Kingsway approach:
7 trusted steps to compliance
The human, financial and environmental impact of ineffective ligature-resistant products and strategies can be considerable.
Kingsway’s 7-Step approach is designed to reduce suicide risks around doors and bathrooms in behavioral health environments.
The national cost of mental illness and suicide is estimated to be up to $70 billion per year in Australia
[Australian Government Productivity Commission, 2020]
Phase One
Relationship
Step 1: Facility Review
- Gaining a complete understanding of the facility, the processes & strategies, and potential risks.
Step 2: Setting the Standard
- Establishing a best practice strategy for ligature resistant products within the facility.
Step 3: Sampling & Approvals
- Providing full-size product samples for the facility and key stakeholders to review, including nursing staff and patient safety managers.
Phase Two
Project Lifecycle
Step 4: Project Specification
- Kingsway’s in-house Project and Design teams come together to define the scope of the project.
Step 5: Manufacture & Delivery
- The specified products are put into production in our Michigan based production facility and delivered to site.
Phase Three
Aftercare
Step 6: Annual Safety Check
- Ensuring the ligature resistant strategy is continuing to deliver life-saving benefits.
Step 7: Compliance Review
- Supporting the facility in keeping their systems up to date and ensuring continued compliance.
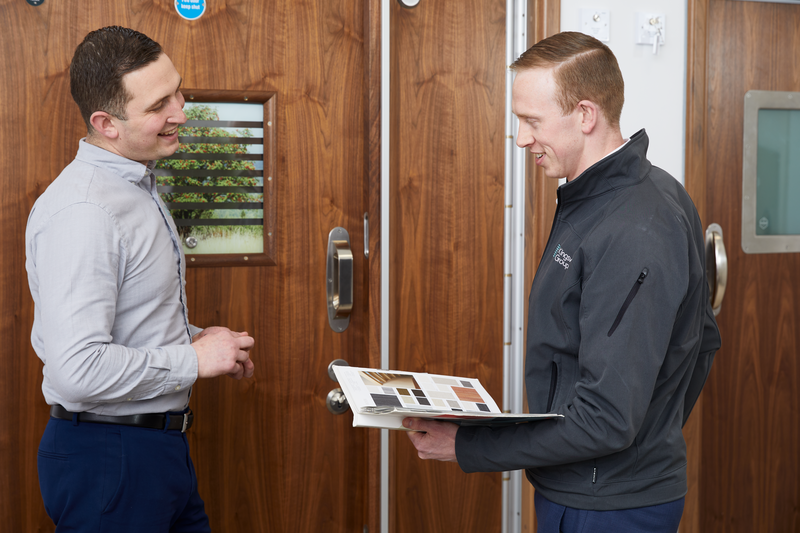
Want to learn more about our de-risking process?
Why not book an online demonstration?
We’ll guide you through our process in full and provide you with live demonstrations of our risk-reducing solutions at a time of your convenience.
Simply request a demonstration below and we’ll be in touch! Or give us a call, we’re always happy to speak.
Browse our product range
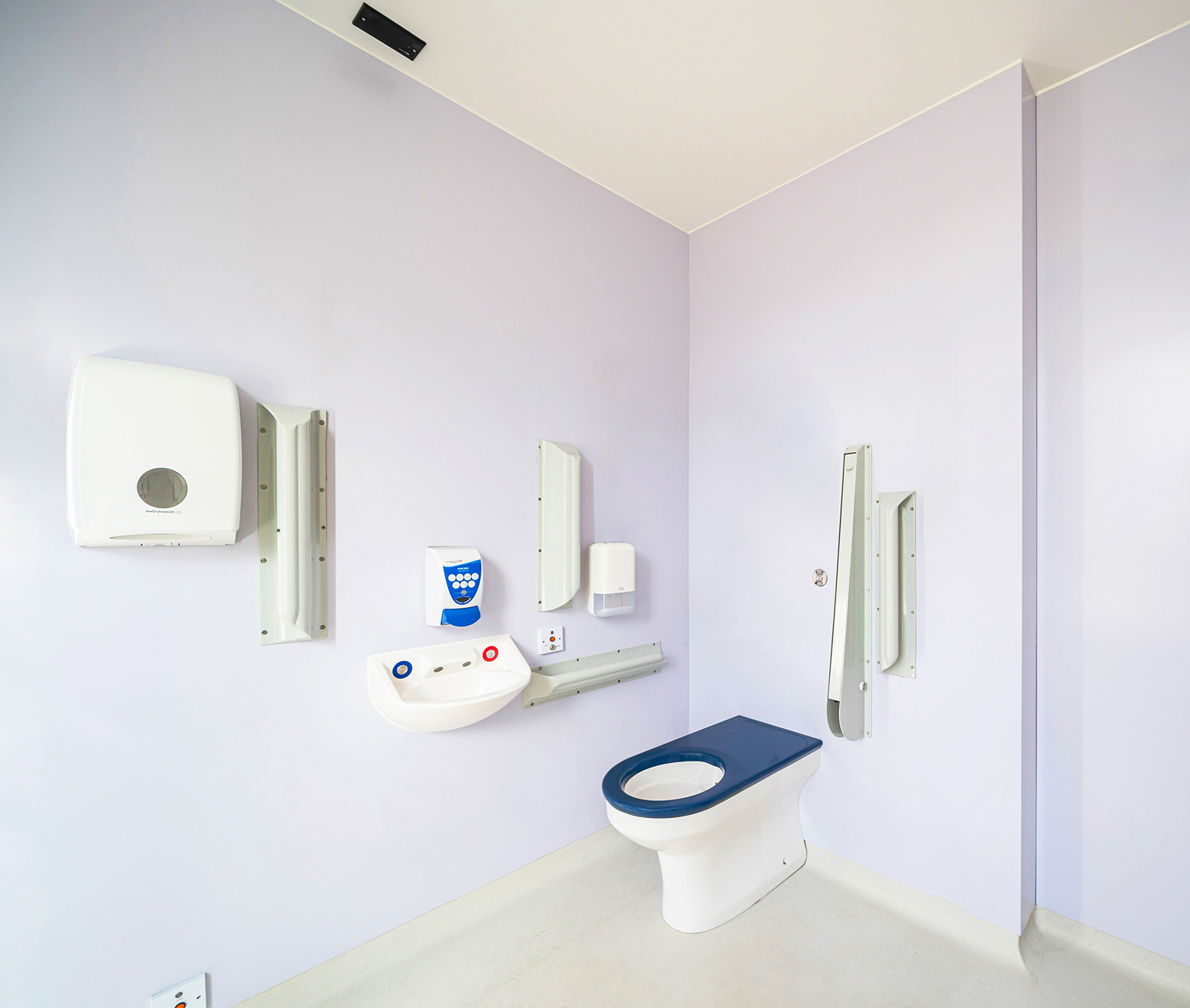
Anti-Ligature Washroom Accessories
Browse products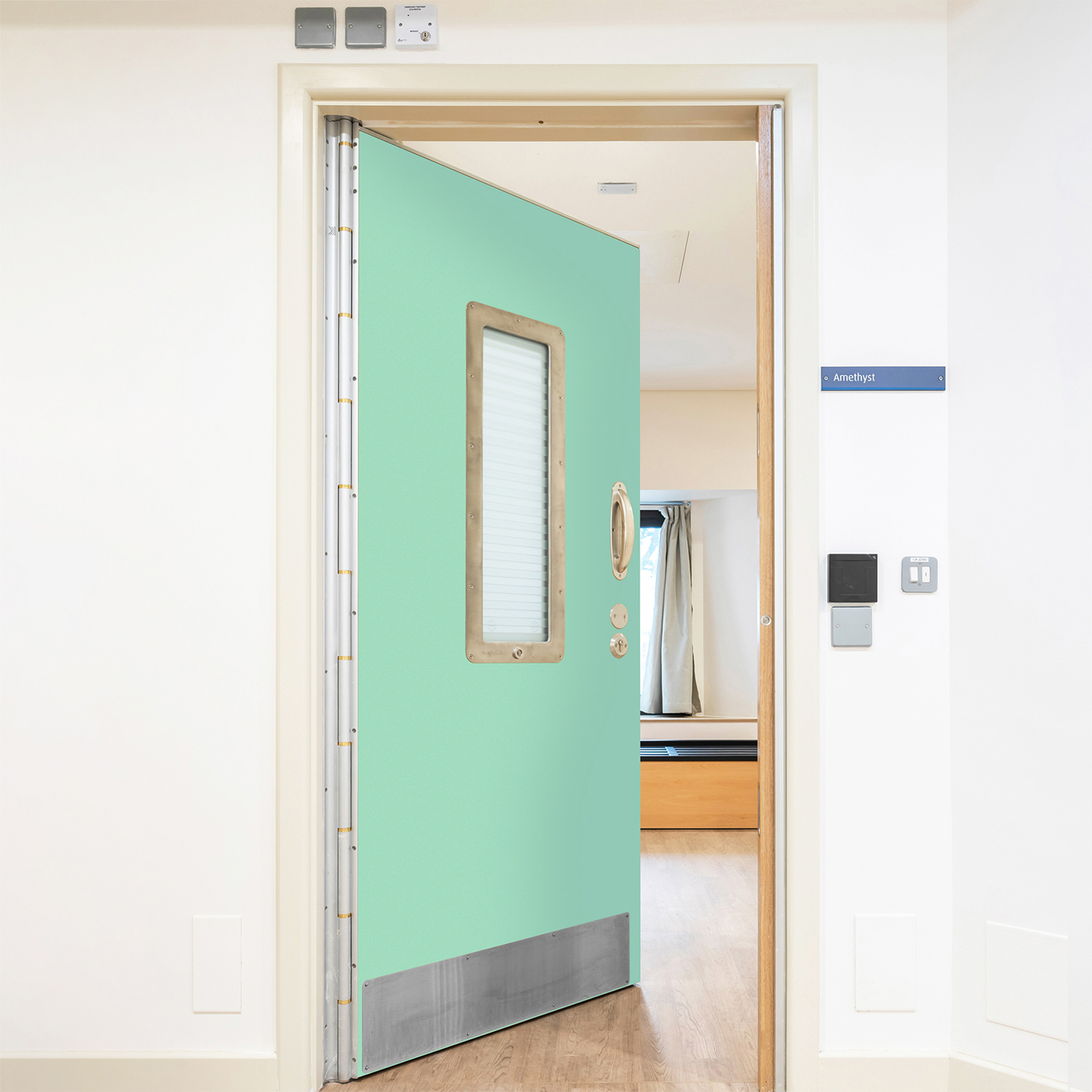
Anti-Ligature Door Systems
Browse products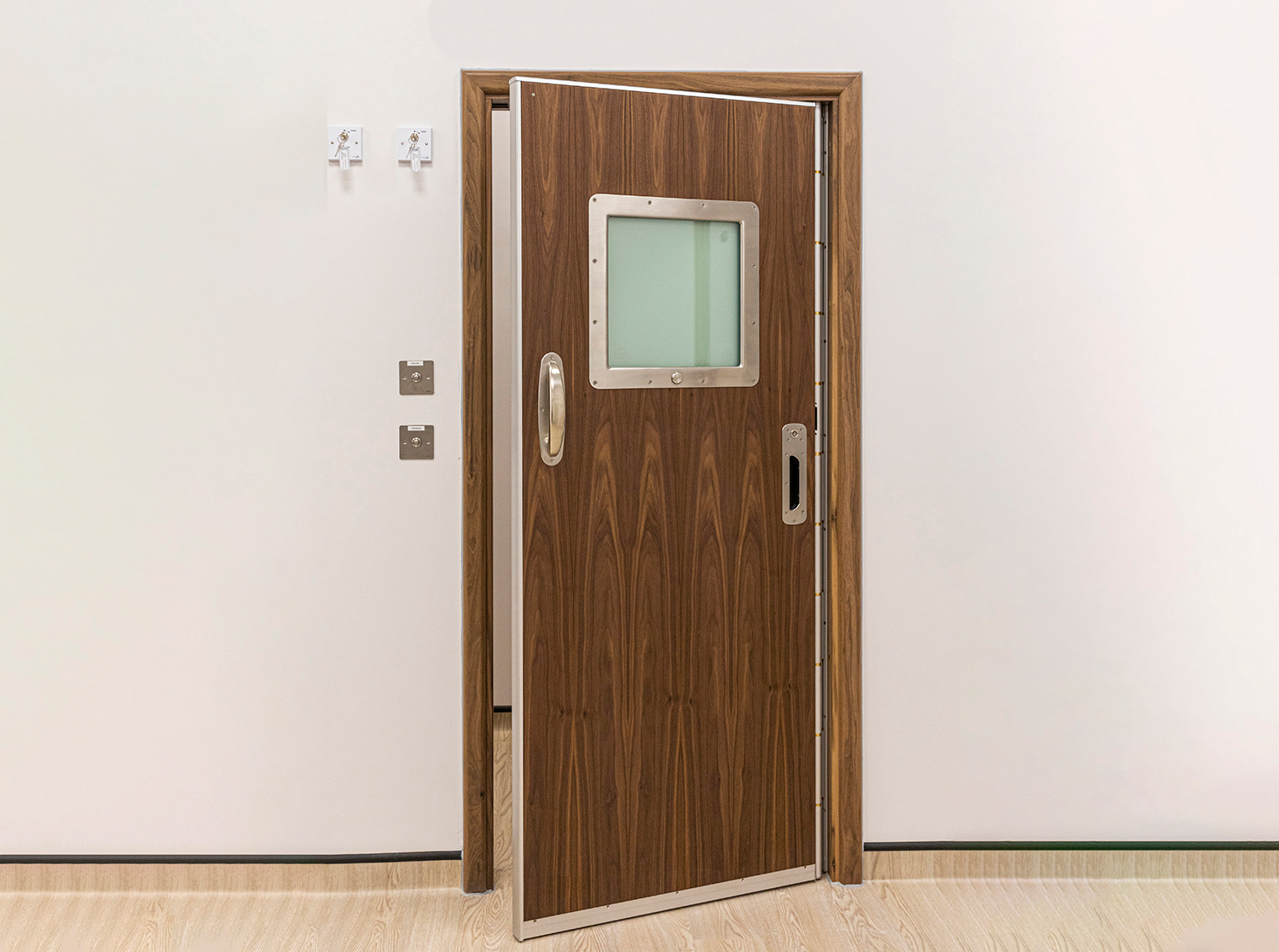
Ligature Alarmed Doors
Browse productsRead more...
- General
- 2 min read